Process Flow Management
Through ECOUNT, the company can seamlessly apply the production flow and
easily understand the progress status of each process.
Optimized process
management system tailored to
the company's production flow
- Register unlimited number of warehouses and factories.
- Monitor inventory status across multiple factories and
warehouses real-time.
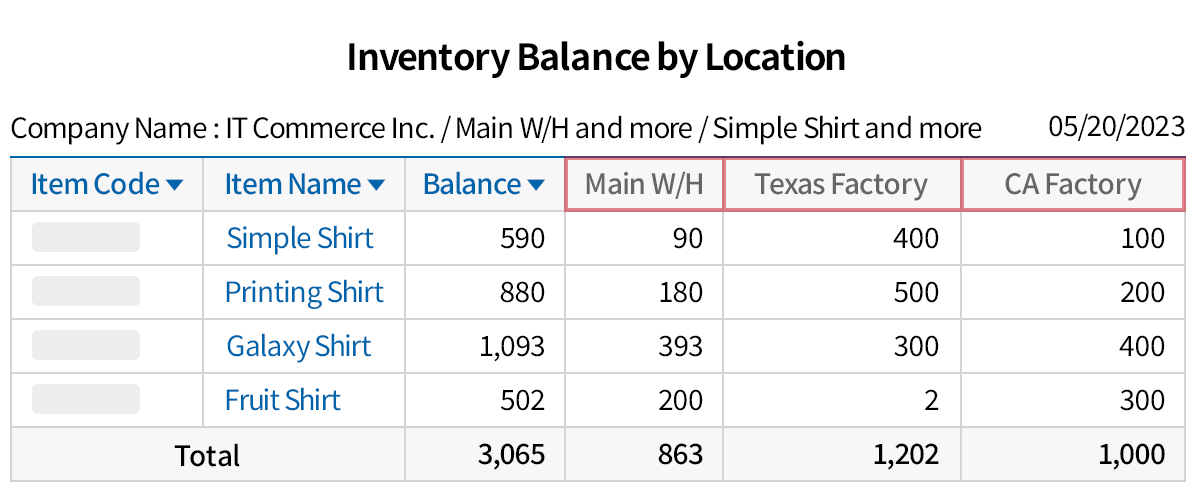
Track inventory
automatically to enhance
operational efficiency
- Inventory transactions for all processes are
automatically managed when entering production slips. - Quantity of raw materials input into production
decreases while the finished goods increase based on
the BOM.
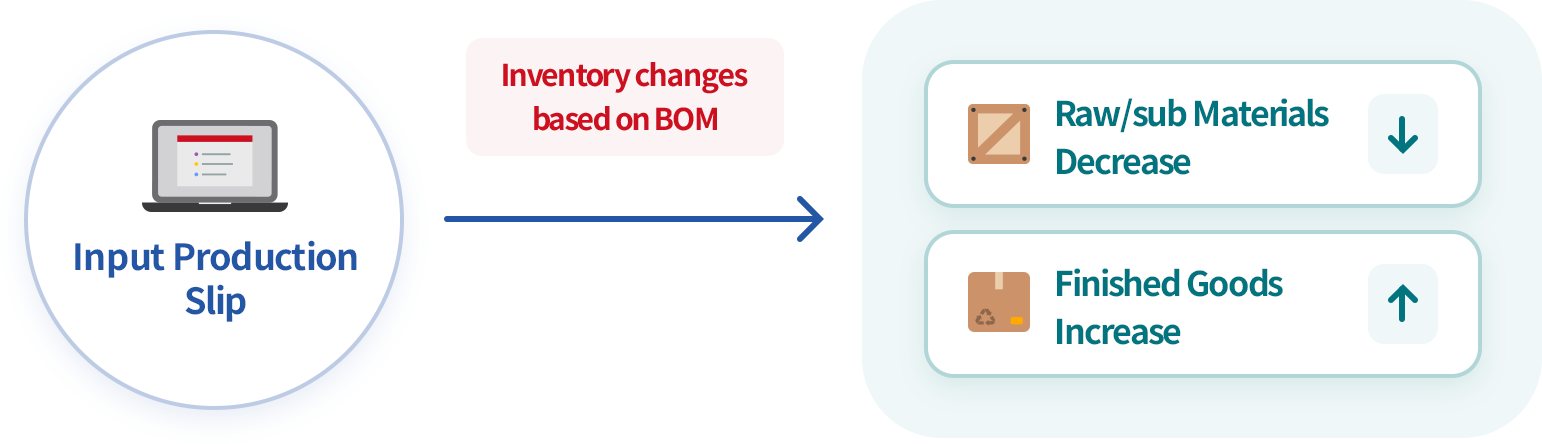
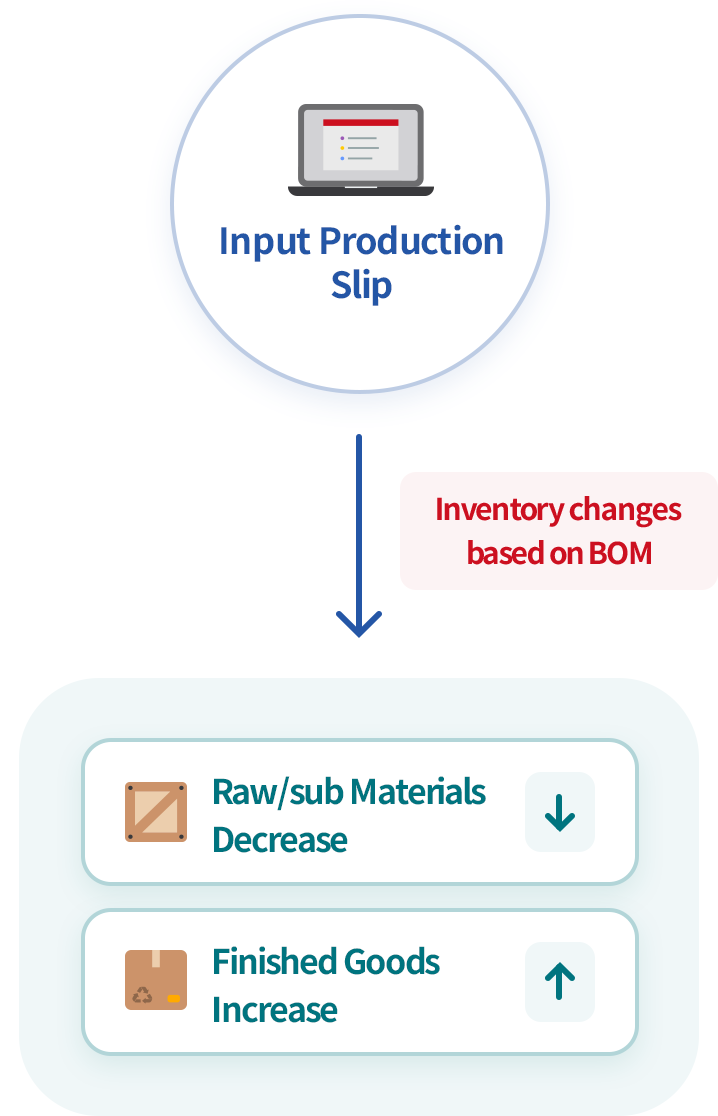
Easy-to-track production
site work management
- Record and review the equipment or manpower
inputted at each process. - Compare the standard work time and actual work
time of production based on the BOM to verify the
efficiency of the work.
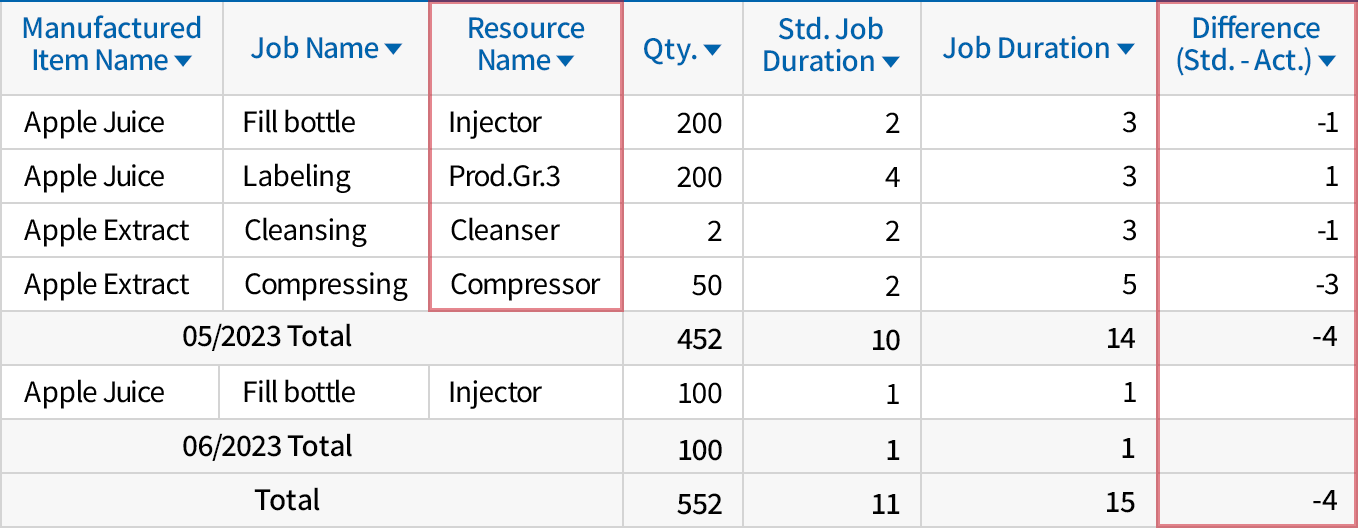
Various production reports
- Compare the instructions given for the tasks with the actual production results to
understand the production progress status by process, in real-time. - Identify the yield differences by process by comparing the expected consumption
quantity based on the BOM with the actual consumption quantity.
Managing outsourcing partners
- Incorporate the production processes of outsourcing partners into the company's workflow for effective management.
-
Include outsourced factories in the company's processes to manage inventory transactions and to track production status effectively.
-
Handle accounting for goods payment and outsourcing processing fees based on whether it is a paid or unpaid supply when receiving the deliveries from the outsourcing partners.
-
Systematically manage the entire process from placing an order to production receipt and payment settlement.