Cost Management
ECOUNT automatically calculates the cost and profit
according to the purchase, production, and sales transactions.
How to calculate the cost
correctly for the company
- Choose the desired cost calculation method (average cost
method, FIFO, last purchase cost method) to calculate the
manufacturing cost of products on a monthly basis. - Choose whether to calculate based on outsourcing costs
pre-entered during item registration or actual outsourcing
costs to reflect on the cost. - Labor costs, expenses, import-related expenses, etc. can be
reflected in the cost by process of item.
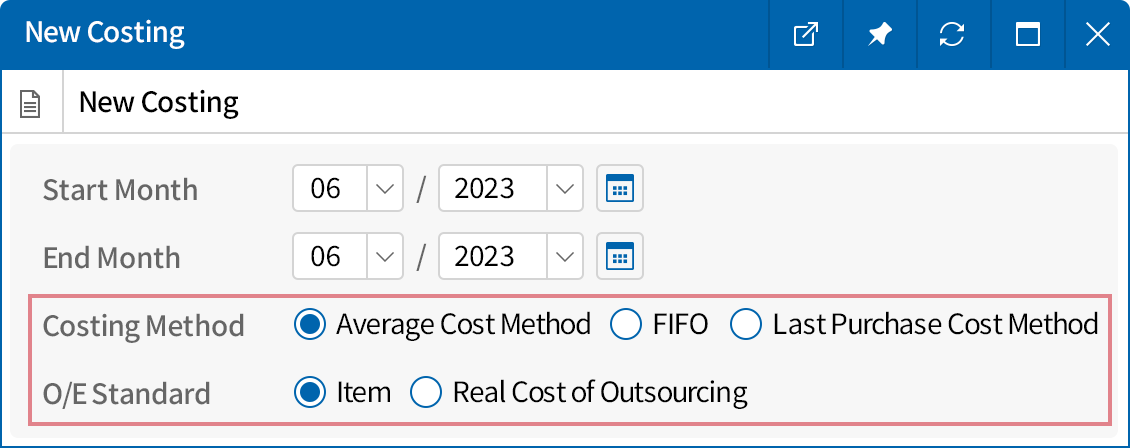
Pre-cost vs. Actual cost
- Compare the pre-estimated cost based on the BOM of item before production and the actual cost after production.
- Analyze the reasons for discrepancies in each category, such as differences in material cost, consumption quantity, etc.
